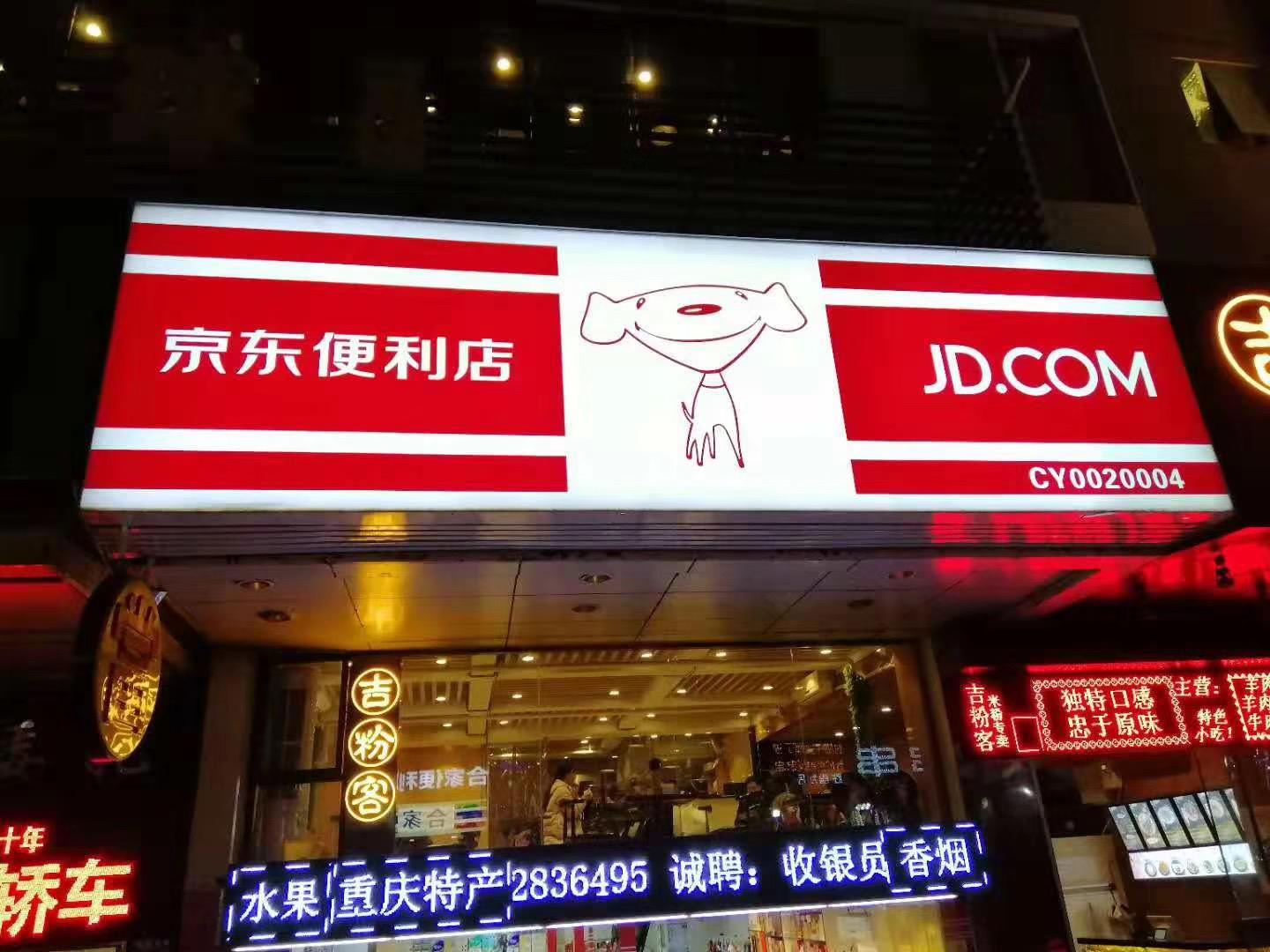
Con respecto al problema del burbujeo que se produce durante el proceso de aplicación de película de las cajas de luz de 3M, Se estima que la mayoría de los amigos que se dedicaban a este trabajo deberían haberlo encontrado. The following will specifically introduce this work for you. Let’s take a look together!
-
Bubbles were generated during the film application process of 3M light boxes. If there is too much detergent used for this kind of bubble, it is inevitable. After a long time (after 3 hours), the film application reaches permanent viscosity, and there is almost no way to repair it; if there are a small number of small bubbles generated by the dry application method or the wet application method, a special squeegee can be used to gradually gather the small bubbles together to form a larger bubble, and then use an exhaust pen to make a small hole at the bottom of the bubble, and use the thumb surface to push the air out.
-
Bubbles caused by the problem of the material to be pasted. Many colleagues have reported that sometimes the effect is very good after the film is applied, but after a period of time, it will be found that there are many small bubbles on the film, and more and more. This situation is generally caused by the quality of the material to be pasted. For example, acrylic panels, ABS materials, etc. that contain recycled materials. There are a large number of unstable plasticizers and gases overflowing in these materials, resulting in many bubbles appearing afterward.
-
Bubbles are generated by thermoforming. Some mid-range films also have extremely good ductility and can be completely “applied first and then thermoformed”. In this way, it is very easy to solve the processing of complex thermoformed graphics, such as the storefront of Kodak’s EXPRESS photo developing store across the country. But if the method is not proper, many small bubbles will also be generated during the thermoforming process. When encountering this situation, just pay attention to one point. When we apply the film to the acrylic panel by the wet application method, no matter how many times we scrape, it is impossible to completely scrape the water between the film and the plate. At this time, an additional procedure needs to be added, that is, put the film-plated plate that has scraped the water into an oven at 70 to 80 degrees Celsius bake for 3 to 4 hours, and then perform heated thermoforming after the water is completely dried.